Lost wax casting steel parts for truck
Product Description
Mingda uses this process exclusively. Wax is injected into an aluminum die to create a wax pattern;. These wax patterns are then assembled onto a tree; which is repeatedly dipped in a ceramic slurry that, after drying, hardens into a mold. The wax is melted out, the mold is preheated and the metal is poured in. The resulting casting has an excellent surface finish of around 125 RMS, crisp lettering and minimal machine stock. This process is perfect for highly visible or highly machined parts. Tolerances can be held to +/-.005 in most cases.
Advantages: excellent overall appearance, machining reduced or eliminated, can cast very thin walls, good for prototypes, economical tooling costs.
OEM and ODM service
Technology Terms :
1. ISO9001 & TS 16949 Certified.
2. Products Material Standard: ISO, GB, ASTM, SAE, ISO, EN, DIN, JIS, BS
3. Product weight range: From 0.5 kg to 100 kg;
4. Main process:
- Casting Process: Investment Casting, Lost wax Casting, Water Glass Casting, Silica Sol Casting, etc,
- Further Production Process: Deburring, Sandblasting, Machining, Heat Treatment, Surface treatment, etc.
5. Material Available:
- Carbon Steel: 10#, 15#, 20#, 25#, 30#, 35#, 40#, 45#, 50#, 55…etc.
- Alloy Steel: 15Mn, 40Cr, 42CrMo…and other alloy steel.
- Stainless Steel: SUS304, SUS316, SUS316L, SUS410…etc.
6. Available software: Pro/E, Auto CAD, Solidwork.
7. 2D & 3D Drawings (Igs, PDF, JPEG, DWG, CAXA, UG, Stp, etc.) could be made and provided based on the samples.
Further Production Proces :
1. Precision Machining equipment: CNC, Lathe machine, Milling machine, Drilling machine, Grinding machine, and so on;
2. Heat Treatment: annealing , carbonization, tempering, quench, normalization and surface tempering
3. Surface treatment: Powder coating, Chrome plating, Painting, Sand blasting, Nickel Plating, Zinc Plating, Blacking, Polishing, Bluing, etc.
Tooling and mould
1. Mould life: usually semi-permanent.
2. Tooling Leadtime: 15-25 days, depending on the structure and size.
3. Tooling & mould maintenance: Be responsible by Evergreen Machinery.
Quality Control
Our factory


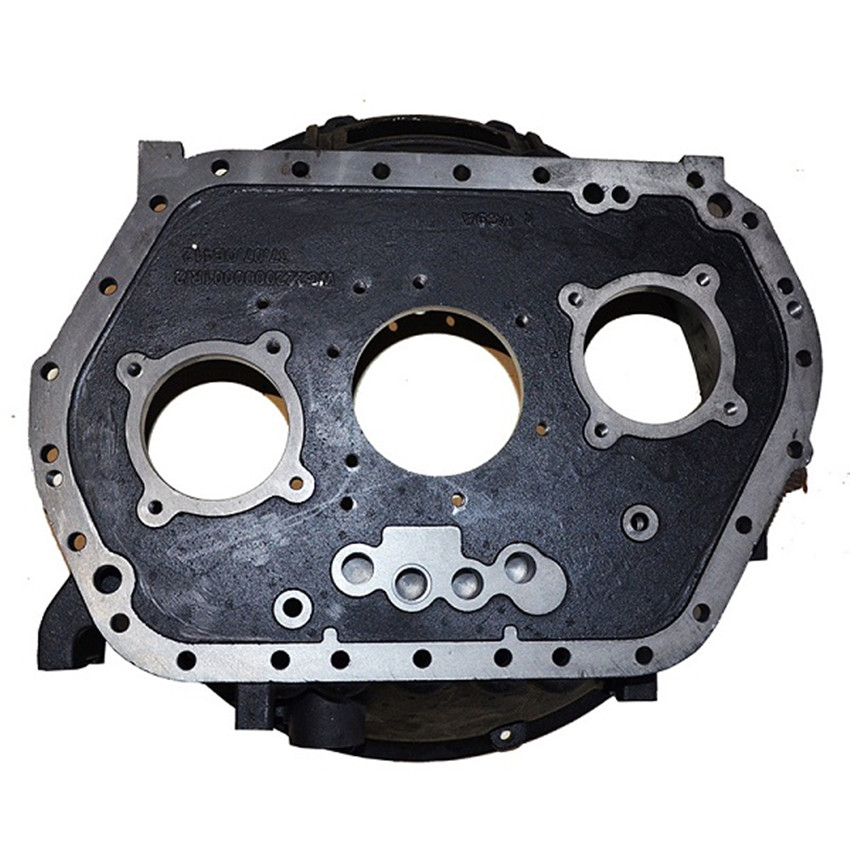
1. Quality control: The defective products rate is less 0.1%.
2. Sample and pilot run will be given 100% inspection during production and before shipment, Sample check for mass production according to ISDO standard or customer requirements
3. Test equipment: Spectrum Analyzer, CMM, Hardness test equipment, Tension test machine;
4. After-sales services are available all time.
5. Quality situation can be traceable.